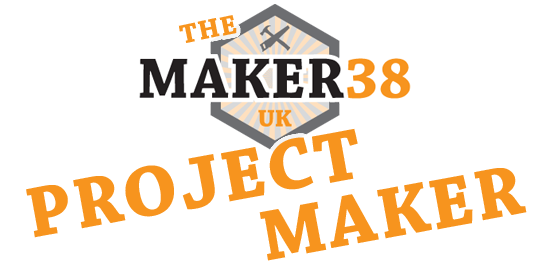
So after many stolen minutes trying to get design work and scripting done during any spare moments I could find, I’ve finally managed to complete my online project that seemed to take an eternity.
The Project Maker is an online generator for makers and DIYers that will randomly select a project idea for you to build.
I’m not always able to find time to make in the workshop as I already have a full time job, so this is my alternative offering to the community.
Along with the project idea you’ll get a materials and tools restriction which is there to challenge your creative thinking. The Project Maker should act as the initial springboard for your build idea and get you to think around the problems that the material and tool restrictions provide.
In theory this should lead to every maker developing a completely unique design every time so be sure to share the project with others and applaud their efforts whilst having some fun with it.
Of course there’s a few that will always look for the additional challenge which you can easily do by adding a time restriction. Just be sure to share the project specific link if you do.
Currently there’s 85 projects, but with the material and tool restrictions there’s something like 20,000+ unique combinations, so hopefully there’s something for everyone. I also hope to add more in the near future!
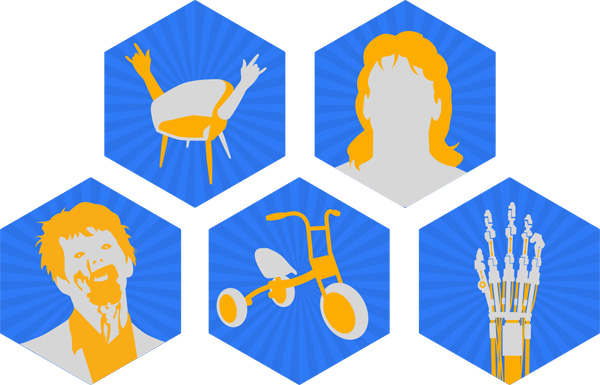
The combinations have limitations to prevent silly pairings like getting hammers as the tool to use with glass. That wouldn’t be the greatest of builds regardless of the project idea.
There’s also a probability factor for each of the three aspects to increase the chance of getting something that is viable to build for most, but it is still a random selection so you will still get some interesting choices coming your way.
With a few of the projects I am adding “inspiration” links to other makers whose work I think is worth drawing inspiration from as a starting point. I’m still seeking permission from a number of makers as I’d rather get permission than just post randomly without their consent. Any links you do see I have gained permission for.
Go generate a project nowIn your project, if you happen to draw inspiration from anyone in particular, then be sure to credit them if you post anything online and maybe even let them know about what you’ve done. Makers are generally a very friendly bunch.
You can also use the project specific link to share with others.
Lastly, I built this as something fun for anyone to enjoy, but if there’s anything not quite right, then feel free to get in touch so that I can improve or amend things. I believe in trying to be fair and doing things right so if any attribution needs correcting, then I’ll sort it.
Enjoy!